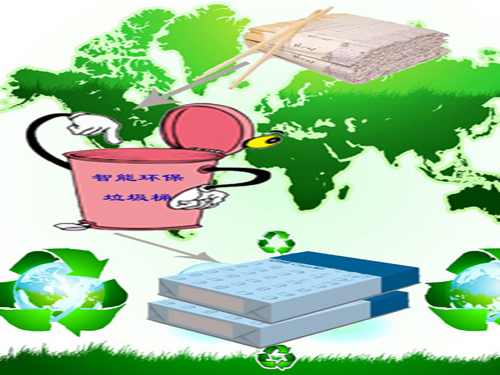
Recently, the China Printing and Dyeing Industry Association held a new product conference in Yizheng, Jiangsu Province, and launched the “New Intelligent and Environmentally Friendly High-speed Effluent Dumping and Mixing Machine†produced by Jiangsu SEG Textile Machinery Co., Ltd. The machine complies with the development trend of “high-speed, intelligent, continuous, energy-saving, and environmental protection†in the future dyeing and finishing equipment, and the price is only 45% of the imported equipment.
The combination of desizing, scouring, and rinsing to fit the short-flow pretreatment process is the basis of the fabric pretreatment process and plays an important role in stabilizing and improving the product quality of subsequent processes. . However, an imported decoction and bleacher combined machine is expensive, about 13 million yuan or so, and the industry has been looking for alternatives that are relatively inexpensive. Recently, the new intelligent environmental protection high-speed decoction and bleaching combined machine launched by the China Printing and Dyeing Industry Association at the new product launch conference only needs 5.8 million yuan***, the price is 45% of imported equipment, and its performance and production product quality can completely replace imported equipment. It conforms to the development trend of “high-speed, intelligent, continuous, energy-saving, and environmental protection†in the future dyeing and finishing equipment.
The new decantation machine is the latest product of SEG’s export to the Turkish market. This type of product was first released in the country. This machine is suitable for the continuous process of continuous desizing, scouring, bleaching, etc. of cotton, polyester, hemp and their blended fabrics. It adopts automatic feeding system, water and electricity consumption and pH value intelligent control technology, and has a high level of intelligence. . The product is totally enclosed design, the surface of the cabinet is heat-insulated, the water-saving and net-cleaning effect is good, and it has high-efficiency, energy-saving and environmental-friendly effects, conforms to EU environmental protection standard ROHS, and passes the EU CE safety certification.
In manufacturing, all laser cutting and CNC machining are used to ensure the precision and finish of the parts. In terms of core configuration, all of E+L Germany's Laimer Edgers, German Saiwei Motor Reducers, Germany's SIEMENS Inverters, German MAIER Rotary Joints, and British Spirax Sarco Steam traps, NSK bearings, SKF bearings, FESTO cylinders, KEYENCE static elimination devices, etc. There is no difference with imported products and the products are in line with international standards, ensuring the reliability and stability of transmission components and control components.
Use cloth route
SEG's new brewing and bleaching machine has absorbed the concept of combining Benninger technology and equipment from Switzerland, adopting a modular building structure, placing the steam box above the washing tank, and making full use of it without affecting the operation. The space resources of the equipment; the steam box and the rolling mill adopt a fully-enclosed structure, which realizes a perfect combination of the rolling mill and the steaming tank and avoids the loss of steam; the total length of the whole machine is about 36 meters, which is less than the average machine About 20 meters, which greatly reduced the land use area.
The new intelligent environmental protection high-speed decoction and bleaching machine uses a unique cloth route. It is precisely because of this unique "shaped cloth" route design to shorten the length of the entire machine, and the amount of content per unit area has almost doubled. On the one hand, this design improves the washing effect, saves water and steam; on the other hand, it prolongs the time of washing and pre-steaming, which greatly enhances the efficiency of net washing and cleaning and the cooking effect of the fabric, and improves the fabric's Feel.
The design of the steam box is reasonable, which is conducive to the process implementation and manual operation. The steam box is equipped with a self-contained saturated steam generator. Its internal structure is reasonable, and it can make superheated steam and water contact with each other and exchange into saturated steam more efficiently. And its temperature, humidity, pressure, flow control, can accurately adjust the relevant parameters in the steam box, to ensure the stability of the process, thus ensuring the product's verticality, and to ensure steaming under relative humidity, with Avoid fabric burns and air dry printing. The steam heating system is designed to ensure rapid emptying of the steamer during the temperature increase. Because the pre-steaming area has a capacity of 120 meters, it ensures that the fabric can fully absorb heat and heat up before being stacked, so as to achieve the same internal and external temperatures and ensure the effect of steaming. Before the pre-steaming, the unique turning device is designed before entering the roller bed, which can help the fabric to avoid breakage and damage when leaving the roller bed. The steam box adopts roll bed stacking to make relative motion between the fabric and roll bed in the steaming process, which can effectively avoid the generation of cross-stitch printing. The roll cloth capacity is designed to be 4,000 meters. An innovative pneumatic linkage device is used in the steam box to achieve automatic switching during loose pile and tight machining conversion. No parking and window opening are required, thereby reducing labor intensity and streamlining the middle of the switching process. The route of cloth route avoids the process of secondary wear and secondary heating. It not only saves production time, reduces energy consumption, but also improves production efficiency. Stacking alarms are installed at the outlet of the steamer to avoid accidents during the stacking process. The steamer box also specially designed the cooling system of independent intellectual property rights, that is, the automatic shower device and the automatic development device for high doors and windows. The top of the steamer is designed with thermal oil to prevent water leakage at the top.
The main roller and the upper guide roller and the drying drum of the pre-steaming zone of the steam washing box of the machine are all separated by a main drive. Each set of transmission is controlled by a separate gravity sensor to adjust the radial tension of the running of the fabric, ensuring the running process. The low tension. The elastic frame device that regulates the speed of the line uses the design of the guide roller weight, which reduces the radial tension of the fabric during operation, and enables the front and rear unit machines to control through the angular displacement sensor to avoid the wrinkles of the processed fabric. problem.
7 system intelligent transformation
The new intelligent environment-friendly, energy-saving, high-speed decoction and bleacher combined machine has transformed the seven major systems in terms of intelligence.
The five kinds of work required by this machine are all using self-developed and designed automatic feeding system, using the imported German proportional pump to directly set the raw materials according to the recipes set by the process and the pre-set condition values ​​such as the process speed, fabric type, and automatic feeding adjustment. No manual ingredients required. Due to the change of the traditional artificial material and gravity flow feeding method, the labor intensity is greatly reduced, and the freshness of the working fluid and the stability of the process quality are largely ensured; for each key detection system, such as the process Concentration, process temperature, real-time monitoring and automatic adjustment of the process speed are redesigned; the water supply system of the water-washing tank adopts closed-loop control, and the automatic water supply can be adjusted according to the preset speed of the fabric type without manual adjustment, thus avoiding water resources Waste, also reduces the amount of sewage discharge; PH value automatic detection and control system, real-time monitoring of the cloth's PH value, can automatically add liquid adjustment, to ensure that the cloth is neutral; the whole machine adopts the inverter + PLC + touch screen control method, The digital intelligent control mode is realized, which can greatly improve the stability of the process, reduce the labor intensity and human influence factors, and lay the foundation for the realization of all-digital management and distance control in the later stage of dyeing and finishing; , make the fabric roll in the range of deviation within a certain range during the process of rolling the cloth and solve the problem Thicker, easier to raise problems; intelligent management system for water, electricity, gas, material quantification and metering functions, real-time monitoring of instantaneous data, and consumption statistics for a specified time range, which is convenient for problem finding It also facilitates daily production management.
In addition, the dryer design has three major innovations. First, the German Maier steam head, the British Spirax Sarco steam trap, to ensure the stability and reliability of the dryer, fully guarantee the energy-saving effect; Secondly, the drying cylinder uses a spacing type, the main drive to avoid the belt The easy slippage of the transmission and the difficulty of the oil transmission of the gear transmission. Finally, the on-line monitoring of the temperature of the drying cylinder can monitor the temperature of the outlet and automatically adjust the steam flow of the drying cylinder to effectively control the consumption of steam.
Significant energy savings
The new smart environmental protection energy-saving high-speed decoction and bleaching combined machine also performs dazzlingly in terms of energy saving, which is embodied in aspects such as high-speed, high-liquid-low bath ratio, washing, and drying cylinder temperature detection.
SEG's new decoction and bleaching machine adopts high-speed design, with a mechanical speed of 110m/min and a process speed of 100m/min, which can reduce the consumption of water, electricity and steam to a greater extent, save labor costs, and reduce the labor costs. The control unit uses internationally renowned brand products to ensure the stable operation of the equipment. Due to the stable and reliable process effect, the maximum energy saving effect can be achieved. The composite steamer box adopts the form of steam seal on the same side and exits the cloth and fully pre-steamed and then piled on the roller bed, so the temperature and humidity in the steamer are relatively stable and uniform, which provides a very reliable process for the fabric in the decoction and bleaching process. The process conditions are also the key to the high speed of the whole machine. The new combined decanting and bleaching machine achieves a high liquid-to-liquid ratio, with a liquid volume of more than 100%, an automatic feeding system and a uniform feeding method. Because the bath is relatively low, not only save material but also exchange faster. The water washing adopts automatic adjustment and single-point injection of water supply, and the method of washing backwards and serpentine countercurrently by steaming on the cloth to improve the washing efficiency, but also greatly reduces the intake of fresh water and sewage. The amount of emissions. In the detection of the drying cylinder temperature, the automatic adjustment of the steam flow rate was adopted, thereby avoiding the situation of over-baking or baking of the fabric, and its energy-saving effect was very obvious.
Watch Winder For Eight Watches
Quadruple rotors watch winders, have four rotors can hold eight watches to work. And has a built-in smart timer that will wind then rest and repeat the cycle in either clockwise, counter clockwise or bi-directional directions. Quadruple Rotors Watch Winder can hold a wide variety of wrist sizes, increased interior space to accommodate large size watches, microfiber cleaning cloth, microfiber protective storage bag, and a matte black storage box. The watch winder will not only wind your automatic watches but also store it as well. Each watch winder is hand made and developed to wind all popular brands of time pieces. This watch winder use Japanese Mabuchi Motor to work, it's very quiet, even if you're sleeping, leaving it in your bedroom won't wake you up. All the above are the characteristics of our watch
Watch Winder Reddit,Automatic Watch Storage,Rolex Self Winding Box,Single Automatic Watch Winder
GUANGZHOU T.WING-PAK MFG.CO.,LTD , https://www.watch-winder-factory.com