The cotton cleaning process has the characteristics of good uniformity, less impurities and serious static electricity in the milk protein fiber. In the process of opening the cotton cleaning process, the principle of short process, less grasping, more loose and less playing is adopted. Appropriately reduce the speed of each part of the beater, SFA035C mixed open machine only use parallel beaters, skip its porcupine beaters, while the FA106B opener uses a comb to beat to reduce fiber damage. In order to reduce the evaporation of moisture and oil in the lap, the lap of the roll should be wrapped in a plastic film wrapping bag, and the production must be first used first.
In the carding process, due to the serious electrostatic phenomenon of the milk protein fiber and the poor cohesion between the fibers, the phenomenon of winding the cylinder, the doffer and the apron is easy to occur during the production process of the carding process, so the operation speed of each component is controlled to be low, and at the same time To improve fiber transfer and reduce neps, the spacing of each part should be reasonably preferred. Since the milk protein fiber is relatively expensive, the rear process of the carding machine is mainly reduced or not. The company adopts a fully enclosed rear process, and at the same time reduces the speed of the cover plate to reduce the cotton production rate.
When the variety is produced, the humidity of the card should be controlled to a large extent, and the relative humidity is generally controlled at about 70%. In order to improve the quality of the sliver, the principle of “light weight, slow speed and tight gauge†is adopted. In addition, the pressure of the press rolls should be controlled to reduce the damage to the fibers. The drawing process is to ensure that the fibers are evenly mixed, and the two strips are combined in two ways. Due to the serious electrostatic phenomenon in the production process of milk protein fiber, the problem of winding roller and rubber roller should be solved in the drawing process, especially the suction phenomenon between the 1, 2 roller, so the drawing process should be reasonable. Temperature and humidity, the use of separate isolation and humidification measures to ensure the smooth progress of production.
For the characteristics of milk protein fiber, the drawing process should adopt the principle of “heavy pressure, light weight, large gauge, slow speedâ€. In order to improve the dryness of cooked strips, the head adopts a larger drafting ratio of the back zone. At the end, the method of concentrated drafting is adopted to improve the straightness parallelism of the fibers and the uniformity of the strips of the cooked strips.
In the roving process, the surface friction coefficient of the milk protein fiber is small, the cohesion is poor, the fiber is easy to curl, and the roving coefficient should be too large. The roving tension should be controlled to a small extent to reduce the unexpected elongation of the roving and improve the unevenness of the spun yarn and the uneven yarn formation. In order to improve the roving strip, the drafting ratio of the roving rear zone should be controlled to a small extent, and the roving rear zone spacing should be appropriately enlarged. The humidity of the crude process should be increased by about 5% compared with the production of pure cotton. In order to ensure the smooth progress of production, steam humidification measures are adopted.
The spinning process is to improve the quality of the yarn, improve the drying of the yarn, and reduce the yarn defect. The spinning process adopts the process of “large front and rear area roller spacing, small rear area drawing multiple, small jaw spacingâ€. in principle. In addition, in order to ensure the good life of the workshop, the workshop adopts local humidification measures to control the relative humidity of the variety to 68%, so as to reduce the problems of winding roller and rubber roller caused by static electricity, so that a large number of yarn defects appear.
2. Problems and technical measures in the weaving process Due to the low strength of the milk protein fiber, in order to ensure the original elasticity of the yarn and improve the quality of the fabric, the warping process is "medium speed, small tension, low elongation". The principle of “long†is to use variable frequency motor direct drive and column pressure disc type adjustable tension device to obtain constant winding speed and constant tension, thus reducing the breakage during the warping process and the weaving process. Winch and other phenomena.
In the sizing process, the yarn number of the milk protein fiber is relatively small, the strength is low, and the speed of the sizing process is not too high, generally 40 r/min. The sizing machine generally adopts the process principle of “medium speed, small tension, low viscosity and low temperatureâ€. In the case of ensuring the normal operation of the slasher, the tension of each component should be reduced as much as possible, and a lighter grouting force should be used to reduce the elongation of the sizing, and at the same time prevent the sizing excessively causing the yarn to be brittle. The solid content should not be too high. When formulating a slurry formulation, it is necessary to consider the process principle that is both good for impregnation and good for film formation. It adopts high-concentration and low-viscosity slurry, mainly modified starch, PVA and acrylic slurry as auxiliary slurry formula to improve the flexibility, wear resistance and hairiness of the yarn to form the yarn surface. A flexible and smooth serosa, while avoiding brittle fracture.
The weaving process is based on the characteristics of the milk protein fiber, and the weaving machine is preferably a "small tension, small opening, high back beam" weaving process configuration in combination with the weft density of the weaved variety and the fine yarn count. The use of small tension and small openings helps to reduce the breakage of the warp yarn due to friction. However, due to the small opening, the sharpness of the shed is poor. To ensure the clarity of the opening, the tension difference between the upper and lower warp yarns should be minimized. Therefore, the position of the warp beam should be low to reduce the tension of the lower warp yarn. High mastery.
For plain weave fabrics, the same opening time or earlier opening is generally adopted to reduce the warp tension during beating, which is beneficial to the normal operation of the weft yarn, thereby reducing the latitudinal blocking and stopping, and ensuring that the fabric surface is full and flat. At the same time, the friction of the steel sill on the warp yarn can be reduced, so that the warp yarn breakage can be greatly reduced, so that the number of crepe cloth generated by the parking mark caused by the parking can be greatly reduced.
We have our own factory and are dedicated to the manufacture
and wholesales of quality clothing accessories
Production Name: |
Embroidery fabric lace |
||
Material |
Polyester |
||
Payment |
T/T |
||
Color |
customization |
Width |
146cm-150cm |
MOQ |
500yard |
Delivery time |
About 10-20days after confirming the order |
Advantage |
1.High quality with factory price |
||
Usage |
Widely used in home textile lace,girls dress lace,skirt lace, |
||
Package |
1.20-25kgs per paper roll with strong poly bag outside woven bag. |
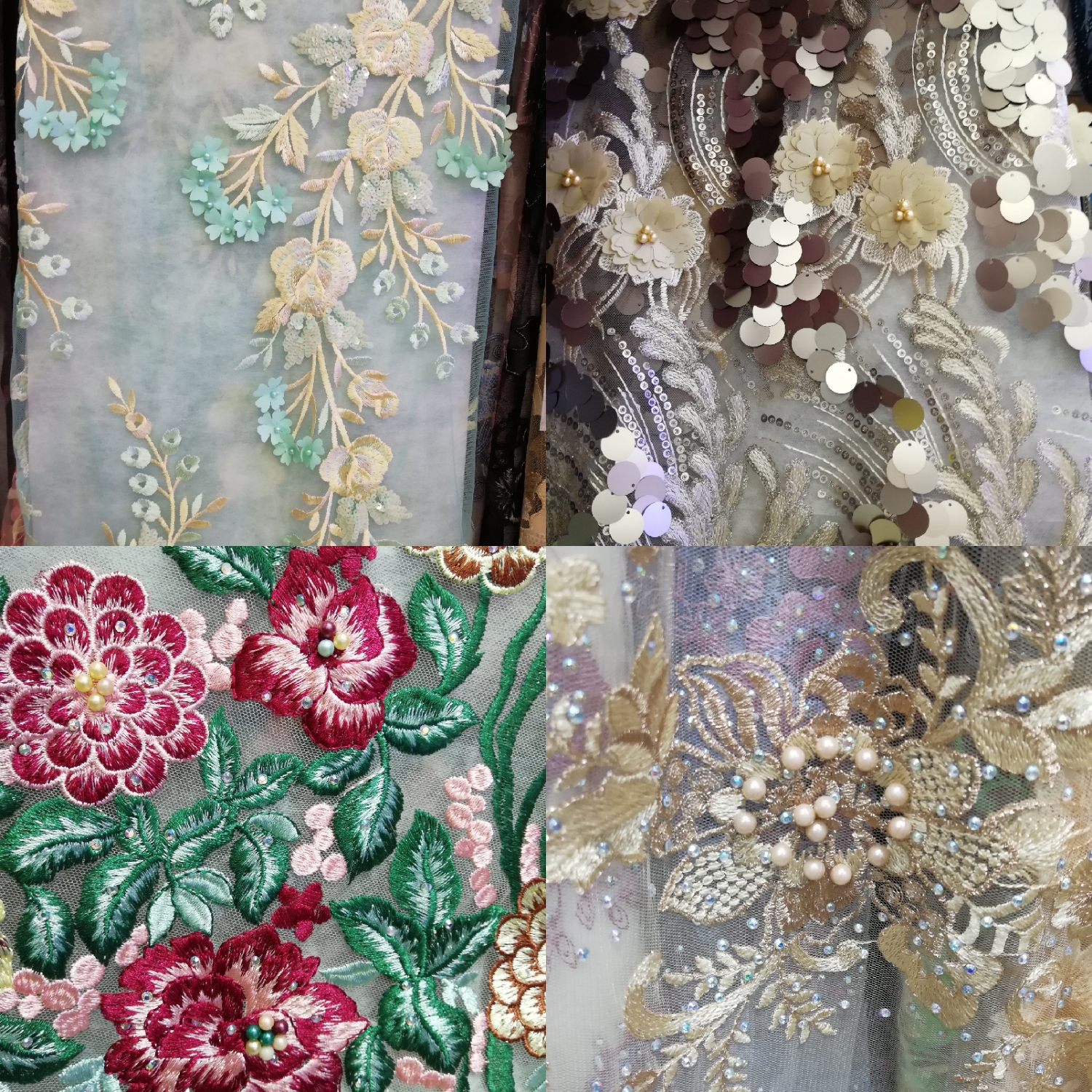
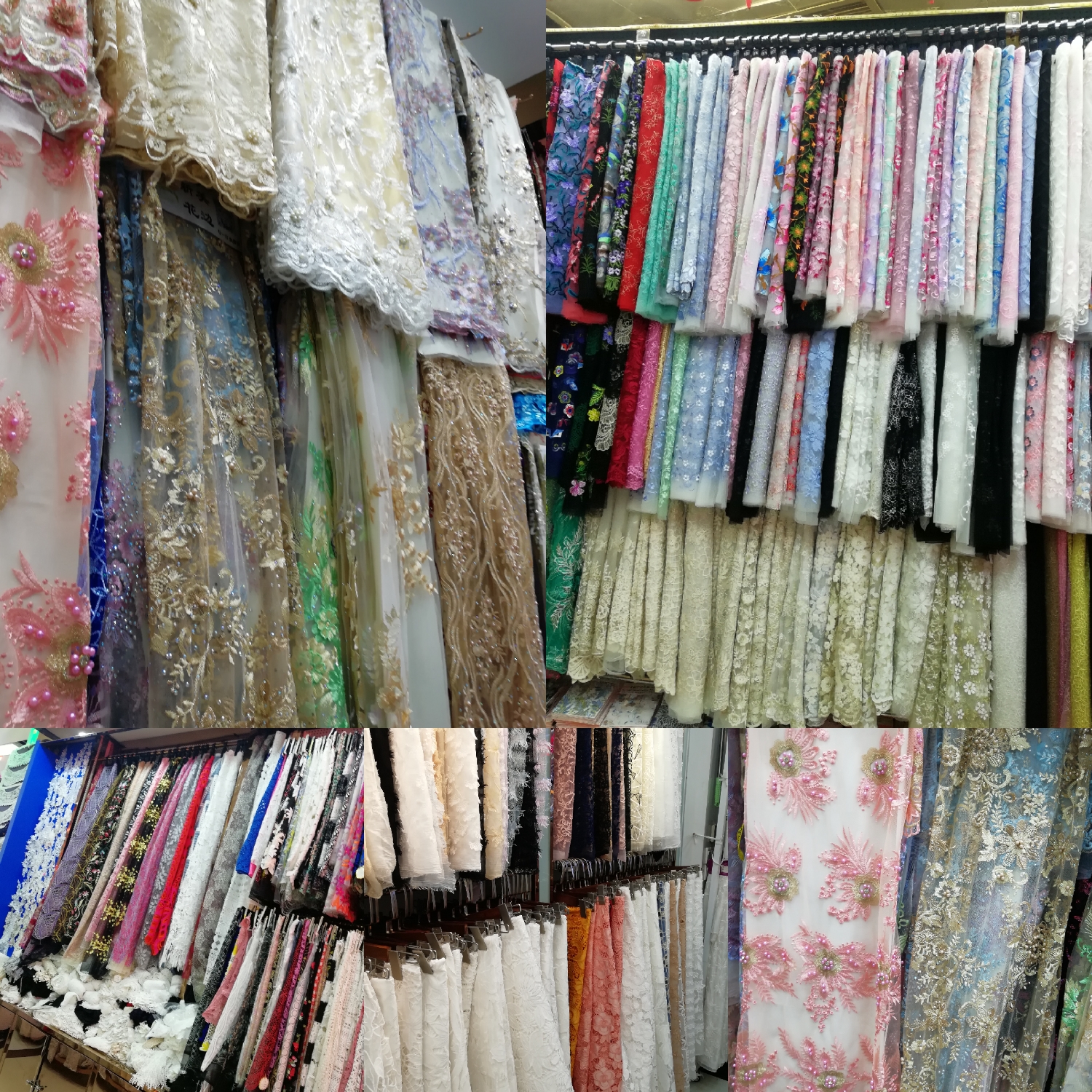
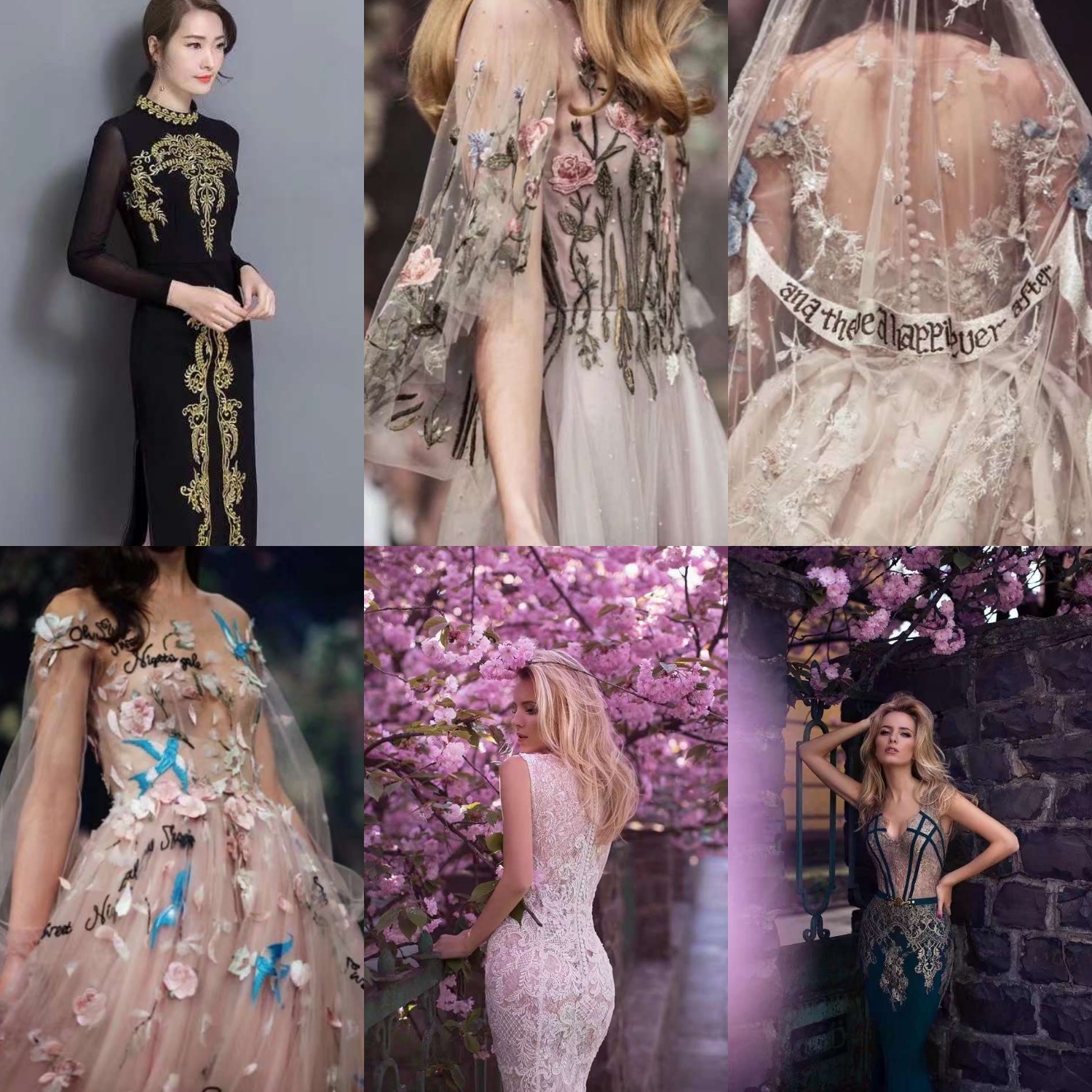

Embroidery Lace Fabric,Embroidered Lace Fabric,Bridal Lace Trim,White Beaded Lace Fabric
DONGGUAN SHITAI ACCESSORY TEXTILES CO.,LTD , http://www.stsewingcraft.com